Мікросхеми, які є майже в кожному авто. Що і як розробляє київський R&D-центр Melexis
Майже кожен автомобіль, що випускається сьогодні у світі, містить 11 типів мікросхем Melexis. Мало хто знає, що частину цих мікросхем розроблено в Україні — в київському офісі Melexis. Тож ми вирішили дізнатися детальніше, що саме та як створюють у R&D-центрі компанії в Києві.
Команда Quality & Reliability
Melexis спеціалізується на розробці мікросхем для автомобільної промисловості. Є розробки й для інших галузей: побутових, медичних товарів, «розумних будинків», геймпадів тощо. За даними компанії, за рік глобально виготовляють понад мільярд мікросхем. Здійснюють повний цикл розробки — від аналізу ринку і постановки технічного завдання до запуску продукту в серійне виробництво.
Офіси Melexis є в 19 країнах. Над кожною розробкою працюють у межах одного офісу, розподілені команди можуть бути лише на етапі підготовки мікросхем для виробництва та на етапі підтримки вже існуючих проєктів. Київський офіс — четвертий за розміром R&D-центр після болгарського, німецького й бельгійського. Він налічує 80 співробітників, 80% з яких — технічні спеціалісти, та святкує цього року двадцятиріччя. Спеціалізація українського офісу — R&D, тут відбуваються всі етапи роботи над продуктом, окрім виробництва, яке зосереджене в Європі та Азії. На аутсорс віддається лише корпусування та упаковка.
Щороку український R&D-центр передає у виробництво
Про процеси в компанії нам розповіли Silicon Lead Sensor Interfaces Володимир Рощук, Test & Industrialization Lead Sensor Interfaces Дмитро Шелковенков, а також Embedded Software Engineer/Team Lead Дмитро Кравченко-Лозня.
Оптичні сенсори, датчики тиску, мотор драйвери — що розробляє київський офіс
Основна спеціалізація — це розробка сенсорів для автомобільної промисловості. Виготовляють мікросхеми, які допомагають вимірювати тиск, температуру, магнітне поле тощо.
Навіщо взагалі потрібні мікросхеми? Як один з прикладів — використання мікросхем дозволило зменшити масу автомобілів: маса ABS-системи, яка запобігає блокуванню коліс при гальмуванні, зменшилась з 4,5 кг (1995 рік) до 450 г (2016 рік), а це загалом впливає на економічність авто. Також без мікроелектроніки було би складно досягнути сучасних норм вмісту шкідливих домішок у вихлопних газах.
«Незважаючи на розповсюджену протилежну думку, мікроелектронні компоненти є значно надійнішими порівняно зі звичайними електронними модулями чи механічними системами. Як приклад можна розглянути привід акселератора. До того як винайшли електронну педаль акселератора, привід відбувався металевим тросом (це дуже схоже на привід велосипедного гальма). Такий механізм є чутливим до забруднення, якого достатньо під капотом; також з часом трос розтягується, тож система потребує постійного обслуговування. У сучасному авто педаль акселератора будується на кутовому датчику позиції (зазвичай на базі ефекту Холла) та електроприводі дросельної заслінки (зазвичай BLDC-двигун). Тож у такій системі немає механічних елементів, які можуть невчасно перетертися. Крім цього, електронна система здатна сама себе діагностувати», — розповідає Silicon Lead Sensor Interfaces Володимир Рощук.
Ідеї розробок найчастіше належать клієнтам. Серед клієнтських проєктів київського офісу — мікросхема, що керує положенням заслінки в системі кондиціонування автомобіля. В цій системі є розгалужена підсистема повітропроводів, що змішують тепле і холодне повітря, аби забезпечити комфортну температуру в авто. В повітропроводах і стоїть заслінка від Melexis, яка регулює змішування повітря. Керується все це з центрального бортового комп’ютера за допомогою однопроводної LIN (Local interconnect network) шини.
Мікросхема, що керує положенням заслінки в системі кондиціонування автомобіля. Image Source
Ще один важливий проєкт — датчики тиску, які використовуються в ABS-системах автомобілів. Ця система безпосередньо пов’язана з безпекою автівки та життям людей. Специфіка датчиків у тому, що вони мають систему самотестування, тобто автомобільна електроніка здатна ще до початку руху зрозуміти, чи все гаразд з функціональністю ABS, чи автомобіль краще не заводити. Найбільші виробники таких ABS-систем є клієнтами Melexis.
Датчики тиску, які використовуються в ABS-системах автомобілів. Image Source
Є в компанії і проєкти, започатковані в її межах: «У нас є система „Великий бар’єрний риф“, яка заохочує інженерів генерувати ідеї. Свою назву вона отримала за аналогією з природним явищем (Великий бар’єрний риф неподалік Австралії — це найбільша система коралових рифів у світі, де завдяки унікальному температурному середовищу та океанічним течіям буяє життя). Будь-який інженер компанії може запостити на сайт ідею продукту, описати, чим це буде корисно на ринку та як буде реалізовуватись. Час від часу ці ідеї розглядаються колегіально, і з’являються нові продукти», — розповідає Володимир Рощук.
Таким продуктом, що з’явився у лавах компанії, є сенсор Time-of-Flight. Він вбудований в інтерфейс керування медіапристроєм за допомогою рухів руки у автомобілях BMW.
Водій за допомогою жестів може збільшити гучність аудіопрогравача, перемкнути радіоканали тощо. Саме сенсор Time-of-Flight розпізнає рухи людини: він генерує картинку як звичайна відеокамера й паралельно з цим вимірює відстань від об’єктиву камери до точок в просторі. Це дозволяє формувати 3D-картинку та розпізнавати положення пальців та руки у просторі.
Команда українських розробників продукту Time-of-Flight
Інші продукти допомагають керувати електроприводами в автомобілі (насоси перекачування палива та мастила, вентилятори тощо), в сучасних електрокарах вони забезпечують вимірювання струмів електродвигуна. У системах внутрішнього та зовнішнього LED-освітлення також використовуються продукти Melexis. Магнітні сенсори, виготовлені в компанії, застосовуються в системах визначення положення дросельної заслінки, педалі акселерометра, колінчастого вала. Розроблені нею датчики тиску є в системах керування впорскування двигуна внутрішнього згоряння.
Компанія має також не автомобільні застосунки, наприклад, системи сенсорів магнітного поля, які використовуються в геймпадах для ігрових консолей. Це ті самі джойстики, за допомогою яких гравці керують ігровими персонажами. Джойстики зазвичай реалізовані на рухомому магніті, а сенсори зчитують положення цього магніту в просторі та дозволяють керувати персонажами.
Системи сенсорів магнітного поля, які використовуються в геймпадах для ігрових консолей. Image Source
У київському офісі Melexis зараз паралельно іде 3 проєкти. Один з них в активній стадії, на початку травня розробники отримали інженерні зразки і тепер досліджуватимуть їх. Замовник — велика європейська компанія, лідер у виробництві систем контролю двигунів внутрішнього згоряння.
Інші два проєкти наразі на стадії завершення. Це два датчики тиску на конденсаторному та резистивному сенсорі та інтерфейс датчика кисню для двигуна внутрішнього згоряння. В планах — збільшити кількість своїх чипів для автомобілів, а також зробити акцент на розробці й виробництві для галузей медицини, геймінгу, «розумних будинків».
Від грубої ідеї до виробництва — як створюються продукти
Зазвичай повний цикл роботи над продуктом триває близько трьох років, утім все залежить від його складності.
У компанії використовують CMOS (complementary metal-oxide-semiconductor) технологічні процеси з нормами 0,18 мкм (мінімальний розмір компонента на кристалі). За словами інженерів, це не найпередовіша технологічна норма, якщо порівнювати з технологіями сучасних мікропроцесорів, але продукти розробляють так, щоб вони витримували досить жорсткі зовнішні умови щодо температури завадостійкості. Деякі продукти містять мікромеханічні системи (MEMS) в якості первинних сенсорів.
Основним матеріалом для виготовлення мікросхем є кремній. Це напівпровідниковий матеріал, який досить широко використовується в електроніці. Провідністю кремнію досить легко «керувати» за допомогою домішок. За рахунок цього у товщі кристала можна створювати просторові структури з необхідними характеристиками (діодний PN-перехід чи MOS-транзистор). CMOS у назві технологічного процесу свідчить про те, що у розпорядженні інженера є польові транзистори двох типів провідності, також декілька типів діодів, резисторів та конденсаторів, а от біполярних транзисторів у цій технології немає. Майже вся схемотехніка базується на польових транзисторах.
Розглянемо process flow у компанії детальніше.
1. Визначення високорівневих вимог до нового продукту
Все починається з аналізу ринку. Потрібно опрацювати ідею на системному рівні й загально визначити:
- з яких компонентів складатиметься продукт;
- які взаємовідносини будуть між компонентами;
- якою буде функціональність продукту;
- чим продукт буде цікавий для замовників та ринку;
- якою буде фінальна вартість розробки та вартість всього продукту.
На цьому етапі працює досить маленька команда з
Володимир розповідає: «На цьому етапі ми інтенсивно співпрацюємо з технічними інженерами компанії замовника, тому що важливо дивитись на продукт більш загально та системно.
Якби ми робили все відокремлено, ми могли б зайти в глухий кут й реалізувати якусь дорогу та складну технічну функцію, що призвело б до значного подорожчання продукту. А якщо вийти на вищий рівень абстракції, то той чи інший аспект можна обійти чисто математично за допомогою програмного коду на системному рівні. Можна не вимагати повної точності вимірів якогось параметру, а спростити за допомогою іншого параметру чи алгоритму обробки сигналу.
Часто наші інженери використовують „ТРІЗ“ — теорію рішення винахідницьких завдань, яку винайшов радянський інженер Генріх Альтшулер у 50-60-х роках минулого століття. До речі, цей підхід досить широко застосовується західними компаніями, наприклад, Samsung навіть має окрему позицію „інженер ТРІЗ“. Я особисто всім рекомендую звернутись до книги Альтшулера про цю теорію „Найти идею. Введение в ТРИЗ — теорию решения изобретательских задач“. Там описано багато нестандартних підходів, які допоможуть вирішити будь-яку технічну задачу та навчать мислити за межами вузько поставленої задачі.
Все це дуже важливо, оскільки помилка на першому етапі є найдорожчою. Якщо ми помилились тут, в кінці буде дуже боляче. Може статись так, що буде витрачено дуже багато ресурсів і грошей, а потім виявиться, наприклад, що тестування неможливе. А якщо ми не можемо тестувати, то не можемо і продавати продукт».
2. Розробка принципової схеми чипа
Після моделювання на системному рівні починають реалізовувати продукт і створюють електричні принципові схеми. Інженери на цьому етапі мають більш вузький пул задач. Все вже визначено, потрібно лише реалізувати систему. Разом з тим процес реалізації продукту триває ітераційно і має елемент творчості, оскільки іноді потрібно переосмислити постановку задачі та щось змінити.
«Найчастіше на цьому етапі відбувається уточнення низькорівневих параметрів продукту (коефіцієнти підсилення сигнального тракту, частотні характеристики тощо). Найбільш часто корекції підлягають технічні рішення, пов’язані із вирішенням проблем електромагнітної сумісності. Досить складно заздалегідь прорахувати реакцію схеми на заваду в декілька десятків вольт на частоті 1,5 ГГц, тож під час моделювання цих процесів доводиться значно корегувати ухвалені раніше технічні рішення.
Моделювання мікросхем відбувається в системі Cadence за допомогою звичних усім інженерам-електронникам SPICE-симуляторів. Принципова схема аналогової частини замінюється SPICE-нетлістом, і CAD-система дозволяє проводити аналіз у часовій чи частотній областях», — розповідає Володимир.
Дизайн продукту складається з двох головних фаз — визначення та реалізації.
Головна мета першої фази — визначення вимог (Requirements) до кожного компонента чипа. Кількість компонентів у кожному конкретному продукті може відрізнятись, але загалом система складається з таких типів:
- цифровий компонент (Digital Component);
- програмне забезпечення (Software Component);
- інтегральна схема (Integrated Circuit Component);
- корпус (Package Component).
В деяких продуктах може бути відсутнє програмне забезпечення, і тоді система працює на цифровому автоматі (Finite-state machine), реалізованому у цифровому компоненті. Інколи чипи не «пакують» у корпус, а безпосередньо «розварюють» на друковану плату чи кристал більшого розміру. В такому разі відсутній корпус.
На цьому етапі загалом працюють архітектори кожного окремого компонента (Component Architect) із залученням головних дизайнерів (Lead Designer) за кожним окремим компонентом.
Коли вимоги до кожного компонента системи чітко визначені, узгоджені між усіма відділами та погоджені системним архітектором (System Architect), фаза визначення закінчується, і починається фаза реалізації.
На цьому етапі працюють два великі відділи: цифрового та аналогового дизайну. Процеси розпаралелені, у кожного напрямку власна специфіка. Цифрові інженери зазвичай використовують мови моделювання схем, вони не малюють їх вручну. Деякі продукти містять мікроконтролер, який теж розробляється інженерами Melexis. Аналогові інженери займаються аналоговими частинами мікросхеми — це системи живлення, первинної обробки сигналів, підсилення, масштабування, фільтрування.
Загалом цифрова частина мікросхеми створюється за допомогою поведінкового моделювання (мови Verilog і VHDL). Далі це транслюється CAD-програмами у принципову схему і топологію мікросхеми. Якщо казати про аналогову частину — це ручна схемотехніка. Її моделювання відбувається за допомогою SPICE.
Software Development
Розробкою ПЗ займається окремий відділ Software Development. До нього входять декілька груп інженерів: спеціалісти, які пишуть софт саме під конкретні мікроконтролери продуктів; ті, які пишуть ПЗ для цифрових платформ та бібліотеки, що підтримують компоненти платформи, доповнюють їх різним функціоналом залежно від вимог Application-інженерів. Ще одна група спеціалістів — ті, які розробляють інструменти. Оскільки в компанії користуються власним мікроконтролером, для нього портували компілятор GCC, створили IDE та інші тули, за допомогою яких можна працювати з залізом. Application-інженери — ще одна окрема група спеціалістів — працюють з продуктом на боці замовника і допомагають йому ним користуватися.
«Деякі продукти містять CPU власного виробництва компанії (MLX-16) —
Розробка ПЗ складається з кількох стадій: Initiation, Feasibility, Concept Design, Design, Tape Out (передача у виробництво). Після проходження цих стадій робота Software-інженерів над продуктом завершується. Але якщо пізніше виявляються баги, то розробники пишуть так звані патчі.
Якщо розглянути сам процес роботи розробників, написання коду займає приблизно 40% їхнього часу. Багато часу витрачається на написання документації, оскільки в automotive-сфері до неї чимало вимог. Після кожного етапу розробки аудитор проводить перевірку, пише свої зауваження. Розробники самі тестують свій софт, окремого відділу, який займається тестуванням ПЗ, немає.
Існують Integration-тести — коли софт тестується на готовому продукті, якщо є така можливість, або на цифрових симуляторах. В компанії існують спеціалісти, які можуть зробити повну цифрову симуляцію продукту до того, як його відправлять на виробництво. Це допомагає перевірити, як софт взаємодіятиме з цифровою та аналоговою частинами майбутнього продукту.
Загалом розробники постійно взаємодіють з цифровими інженерами та mixed signal дизайнерами. Цифрові інженери надають Hardware to Software Interface, за допомогою якого, власне, софт пов’язується з цифровою частиною продукту. Mixed signal дизайнери надають середовище, в якому софт тестується, а також запускають Integration-тести.
Пишуть здебільшого на мові С, часто використовують також Assembly language (для дебагінгу). Намагаються оптимізувати код, написаний на С.
Product verification Engineers перевіряють сотні параметрів інтегральних схем, перед тим як вони потраплять в авто
3. Трасування топології
Після того як принципова схема розроблена, її необхідно транслювати у фотошаблон для виготовлення кристала. Власне, цей етап досить схожий на трасування друкованих плат, але кількість шарів може налічувати кілька десятків. Для створення гарної топології потрібно також звертати увагу на всі три виміри в просторі та паразитні компоненти, які утворюються між сусідніми структурами (відстань між сусідніми структурами вимірюється частками мікрометра).
Топологія цифрової частини генерується CAD-системою, а от аналогова частина трасується в напівавтоматичному режимі. Тополог аналогової частини за допомогою CAD-програми розставляє компоненти та проводить зв’язки між ними. Автоматичні трейсери можуть використовуватись на етапі з’єднання на міжблочному рівні, коли необхідно прокласти багато довгих паралельних трас.
Так виглядає топологія кристала в CAD-програмі
4. Виробництво кремнієвих пластин
Пластини разом з чипами виробляються в іншій компанії — це один з етапів, який Melexis віддає на аутсорс за кордон:
«У мікроелектроніці є два типи компаній: ті, що мають власні потужності виробництва, та fabless-компанії, в яких не існує власних потужностей і вони замовляють це в інших фабрик. Ми є fabless-компанією, оскільки виробництво мікросхем досить дороге та складне технологічно. Якщо є фабрика, яка цей процес налагодила, то зробити замовлення у них вигідніше», — пояснює Володимир.
5. Багаторівневе тестування під час серійного виробництва
Фінальне тестування перед виробництвом відбувається в київському офісі. А ось тестування на пластині здійснюється безпосередньо на виробництві. Наприкінці готові мікросхеми ще проходять етап кваліфікаційного тестування в Києві.
Хоча повноцінних тест-машин, як на виробництві, в Києві немає, мікросхеми перевіряють на спеціальних сетапах вручну (за допомогою хендлерів — машин, які переставляють чипи в тестері). Зараз через карантин інженери не можуть полетіти до іншої країни для відладки, тож особливо важливо, що є змога проводити дебагінг в Києві, щоб відправляти на виробництво майже готове рішення. Але, звісно, зручніше та ефективніше проводити відладку безпосередньо на виробництві, ніж віддалено. З цією метою туди від компанії зазвичай їде інженер, який розробляв мікросхему — так було до 2020 року.
Патчинг друкованої плати для cетап-верифікації мікросхеми
Багаторівневе тестування на виробництві починається, щойно отримають з фабрики пластини з виготовленими на них мікросхемами. Після оптичної інспекції оператори завантажують пластини до спеціальних машин-проберів. Ці машини позиціонують контактні площадки мікросхем під спеціальними голками, що забезпечує електричний контакт між кожним виводом мікросхеми та спеціальною печатною платою. Ця плата з’єднана із тестером електричних сигналів, який за допомогою спеціальної програми виконує перевірку аналогових та цифрових електричних параметрів: напруги, струму, опору, частоти, цифрових послідовностей тощо.
Також на етапі тестування пластин виконується дуже важлива операція — калібрування внутрішніх джерел напруги та генераторів тактових частот. Ця операція вимагає доступу до внутрішніх сигналів мікросхеми. Доступ до цих сигналів часто виконується у вигляді додаткових контактних площадок, які не під’єднуються до виводів під час упаковки в корпус.
Після ще однієї візуальної інспекції, яка підтверджує, що мікросхеми не було механічно пошкоджено під час тестування, пластини відправляються до зовнішніх компаній, де їх розпилюють на окремі прямокутники. Кожен прямокутник за допомогою спеціального клею фіксується всередині металевої основи майбутньої інтегральної схеми та заливається спеціальним компаундом.
Багато компаній, що виконують пакування мікросхем, використовують інформацію щодо результатів тестування пластин. Це дозволяє уникнути витрат на пакування мікросхем, які не є робочими.
Далі мікросхеми в корпусах повертаються на виробництво, і продовжується їхнє тестування. Цей етап виконується за допомогою спеціальних машин — хендлерів, які виконують послідовне підключення кожного виробу до спеціального контактного блоку, що електрично з’єднаний с тестером електричних параметрів.
Зазвичай кожна мікросхема тестується мінімум на трьох різних температурах, що вимагає значних людських та апаратних ресурсів. Так, у компанії використовують сотні високотехнологічних машин, які обслуговуються десятками операторів та інженерів. Все це необхідно для тестування понад мільярда мікросхем на рік.
Такий значний обсяг продукції призводить і до значних витрат на тестування. Так, відмінність усього в 1 секунду у часі тестування продукту може призводити до значного впливу на кінцеву вартість продукту. Тож одним з важливих аспектів роботи кожного тест-інженера є вміння протестувати сотні, а іноді тисячі параметрів за найменший можливий час. Це вимагає поглиблених знань не лише в програмуванні, а й у мікроелектроніці та радіотехніці.
Якщо розглянути обсяг виробництва в компанії глобально, по одній позиції — це 5 млн штук на рік, а на тестування кожного зразка витрачається 5 секунд, тож отримаємо 289 днів чистого машинного часу тестування. А таких позицій виробляється багато. Відповідно, автоматизація та оптимізація тестування є важливим аспектом роботи компанії.
«Наприклад, коли починається розробка, замовник каже, що test-time має бути не більш ніж 3,5 секунди для одного чипа. Коли всі функції написані, проводяться тести, та вони показують, що test-time — 7 секунд. Щоб скоротити цей час, можна попросити дизайнерів винести певні функції всередину чипа. Другий спосіб — оптимізувати програму (код на C++), третій — зменшити усереднення вибірки. Якщо потрібно зменшити ціну чипів, коли вони вже пішли на виробництво, можна взяти дуже велику статистику за 10 млн виробів та поглянути, які тести не виявляють погані чипи. Інженери зрозуміють, які тести не дають інформації, та виключать їх, що зменшить загальний час на тестування», — розповідає Дмитро Шелковенков, Silicon Lead Sensor Interfaces.
Крім того, для прискорення процесу тестування використовується паралельний підхід — це дозволяє тестувати декілька мікросхем одночасно. Для деяких задач у компанії використовується тестування понад 100 мікросхем водночас, однак найчастіше кількість не перевищує 10.
Паралельне тестування вимагає від інженера як знання спеціальних методик програмування, розроблених у компанії, так і розуміння електричних схем, що дозволяють протестувати декілька мікросхем одночасно. В компанії є внутрішньо розроблений фреймворк, який використовується спеціально для тестерів. Саме він дозволяє реалізувати паралельне тестування, тож спеціалістам необхідно його вивчити, перш ніж стати до роботи.
Кінцевим етапом виробничого тестування є візуальний контроль корпусованих мікросхем, що дозволяє уникнути надсилання до замовника виробів, що могли бути пошкоджені під час тестування. Цей етап часто суміщений із пакуванням мікросхем до спеціальних антистатичних трубок, палеток або паперових стрічок.
Після висушування мікросхеми розміщують у спеціальних герметичних пакетах під вакуумом, що дозволяє уникнути негативного впливу зовнішнього середовища до миті, коли корпус буде припаяний до печатної плати.
Саме на етапі тестування на виробництві все має працювати ідеально. А от під час тестування інженерних зразків можуть виявитися помилки в закладених технічних рішеннях (це небажаний сценарій), тож доводиться частину роботи переробляти і шукати більш оптимальні методи вирішення поставлених задач. Справа в тому, що перед тим як проєкт відправляється на фабрику, відбувається симуляція роботи мікросхеми. Але якщо мікросхема досить складна, то симуляція не завжди дає достовірні результати. В результаті, якщо тест-група все ж виявляє, що чип працює не так, як було заплановано, software-інженери можуть змінити прошивку або доведеться взагалі робити редизайн. Наприклад, якщо чип не витримує електричний розряд або надто чутливий до перешкод.
«Етап кваліфікаційних випробувань є також дуже важливим. Аби мати можливість продавати наші продукти автовиробникам, ми маємо довести, що наша мікросхема є надійною. Маємо гарантувати строк експлуатації
За 2000 годин ми можемо екстраполювати, якою буде поведінка нашого продукту через
Калібрування термостріму. Тест-відділ
Вимоги до електронних компонентів у автомобільній промисловості значно жорстокіші, ніж для компонентів побутової техніки. Так, наприклад, діапазон температури для експлуатації побутової техніки у більшості випадків не перевищує 0..+60 °C. Для мікросхем, що встановлюються поблизу двигуна внутрішнього згоряння, цей діапазон може сягати −40..+150 °C або навіть більше.
При цьому вимагають тестувати кожен компонент автомобіля на всьому температурному діапазоні, бо від його функціонування може залежати здоров’я або навіть життя людини. Також згідно з автомобільними стандартами виробники мають зберігати протоколи тестування кожної мікросхеми упродовж усього терміну експлуатації автомобіля.
Коли всі етапи завершено, мікросхеми відправляються замовникам, які реалізують свої системи на базі продуктів компанії.
Які виклики стоять перед інженерами
Кількість стандартних (бібліотечних) та універсальних блоків, які можуть використовуватись в реалізації фінального продукту, досить обмежена. Є підсистеми, які можуть використовуватись без змін, але вимоги до різних продуктів досить різноманітні, тож кожен новий проєкт вимагає значної модифікації стандартних блоків (операційних підсилювачів, джерел напруги тощо).
При розробці сімейства мотордраверів 8131х виникало декілька важливих викликів:
- Як створити універсальний продукт, що підходить для багатьох замовників, і при цьому знизити його вартість. Коли спеціалісти проаналізували загальні вимоги для систем кондиціювання від різних замовників, то створили узагальнений програмний код, який, з одного боку, задовольнить будь-якого замовника, а з іншого — за допомогою високорівневих інтерфейсних команд залишить достатньо гнучкості. На базі цього коду була створена мікросхема з ROM-пам’яттю, що допомогло зменшити площу чипа в порівнянні з FLASH-версією і, як наслідок, здешевити фінальний продукт.
- Зазвичай для визначення позиції ротора двигуна необхідний зовнішній датчик Холла, але він здорожує вартість фінального продукту. Використовуючи фізичні явища в обмотках двигуна та апаратно-програмний комплекс обробки цих явищ, розробники знайшли метод визначення позиції ротора без зовнішнього датчика Холла — і, як наслідок, інженери отримали SINGLE CHIP SOLUTION, що дуже цінується замовниками.
- Також виникла низка труднощів, пов’язаних з комбінацією індуктивного навантаження та порівняно великих струмів (порядку 1А), що призводить до активації паразитних структур на кристалі, які зумовлені обраною технологією виробництва. Тож тут, як зазвичай, найпряміший шлях не є оптимальним, змінити технологію — недешеве задоволення. Довелось шукати методи боротьби з паразитними струмами на кристалі за допомогою менш дорогих методів. У процесі багатьох експериментів інженери знайшли спосіб, як відвести наведені струми вертикально по кристалу на металічний контакт корпусу. Це дозволило уникнути небажаних ефектів у роботі мотордрайверу без значного здороження фінального продукту.
Над текстом працювали Альона Дєдушкіна та Анна Соха.
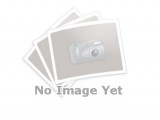

