Сборка домашнего 3D-принтера своими руками: рекомендации из личного опыта
3D-печать и сборка 3D-принтеров — мое хобби и увлечение. Здесь я не буду делиться детальными схемами и чертежами, их более чем достаточно на профильных ресурсах. Главная цель этого материала — рассказать, с чего начать, куда копать и как избежать ошибок в процессе сборки домашнего 3D-принтера. Возможно, кто-нибудь из читателей вдохновится на прикладные инженерные свершения.
Зачем нужен 3D-принтер? Сценарии использования
Впервые с идеей 3D-печати я столкнулся в далеких
Годы шли, все менялось. Примерно с 2010 в продаже начали появляться первые рабочие модели 3D-принтеров. Вчерашняя фантастика стала реальностью. Однако стоимость таких решений, мягко говоря, обескураживала. Но IT-индустрия не была бы собой без любознательного комьюнити, где происходит активный обмен знаниями и опытом и которому только дай покопаться в мозгах и потрохах новых железок и ПО. Так, чертежи и схемы принтеров стали все чаще всплывать в Сети. Сегодня самым содержательным и объемным ресурсом по теме сборки 3D-принтеров является RepRap — это огромная база знаний, которая содержит детальные гайды по созданию самых разных моделей этих машин.
Первый принтер я собрал около пяти лет назад. Моя личная мотивация собрать собственное устройство довольно прозаична и основана на нескольких факторах. Во-первых, появилась возможность попробовать реализовать старую мечту иметь собственное устройство, навеянную фантастическим сериалом. Второй фактор — иногда нужно было отремонтировать какие-то домашние вещи (например, детскую коляску, элементы автомобиля, бытовую технику и другие мелочи), а нужных деталей найти не удавалось. Ну и третий аспект применения — «околорабочий». На принтере я изготавливаю корпусы для различных IoT-устройств, которые собираю дома.
Согласитесь, лучше разместить свое устройство на основе Raspberry Pi или Arduino в эстетически приятном «кузове», который не стыдно поставить в квартире или взять в офис, чем организовывать компоненты, например, в пластиковом судочке для еды. И да, можно печатать детали для сборки других принтеров :)
Сценариев применения 3D-принтеров огромное множество. Думаю, каждый сможет найти что-то свое.
Сложная деталь с точки зрения чертежа, которую я печатал на своем принтере. Да, это просто фигурка, но она имеет множество мелких элементов
Готовое решение vs своя сборка
Когда технология обкатана, ее стоимость на рынке заметно снижается. То же произошло и в мире 3D-принтеров. Если раньше готовое решение стоило просто заоблачных денег, то сегодня обзавестись такой машиной — дело более гуманное для кошелька, но тем не менее не самое доступное для энтузиаста. На рынке присутствует ряд уже собранных и готовых к домашнему использованию решений, их ценовой диапазон колеблется от $500-700 (не самые лучшие варианты) и до бесконечности (адекватные решения стартуют с ценника около $1000). Да, есть варианты и за $150, но на них мы, по понятным, надеюсь, причинам, останавливаться не будем.
Если коротко, рассматривать готовую сборку стоит в трех случаях:
- когда печатать вы планируете совсем не много и редко;
- когда точность печати играет критическую роль;
- вам нужно печатать формы для серийного изготовления деталей.
Очевидных плюсов у собственноручной сборки несколько. Первый и самый главный — стоимость. Покупка всех необходимых компонентов обойдется вам максимум в пару сотен долларов. Взамен вы получите полноценное решение для 3D-печати с приемлемым для бытовых нужд качеством производимых продуктов. Второе преимущество заключается в том, что, собирая принтер собственноручно, вы разберетесь с принципами его устройства и работы. Поверьте, эти знания пригодятся вам в процессе эксплуатации даже дорогого готового решения — любой 3D-принтер необходимо регулярно обслуживать, и делать это без понимания основ может оказаться затруднительным.
Основной минус сборки — необходимость большого количества времени. На свою первую сборку я потратил около 150 часов.
Что нужно, чтобы собрать принтер самому
Самое главное здесь — наличие желания. Что касается каких-то особых навыков, то, по большому счету, чтобы собрать свой первый принтер, умение паять или писать код не критично. Конечно, понимание основ радиоэлектроники и базовые умения в области механики (то есть «прямые руки») существенно упростят задачу и сократят количество времени, которое нужно уделить сборке.
Также для старта нам понадобится обязательный набор деталей:
- Экструдер — элемент, который непосредственно отвечает за печать, печатная головка. На рынке есть множество вариантов, но для бюджетной сборки я рекомендую модель MK8. Из минусов: не получится печатать пластиками, которые требуют высокой температуры, есть заметный перегрев во время интенсивной работы, который может вывести элемент из строя. Если бюджет позволяет, то можно посмотреть на MK10 — там все минусы учтены.
- Процессорная плата. Хорошо подойдет знакомая многим Arduino Mega. Я не заметил минусов у этого решения, но можно потратить на пару долларов больше и приобрести что-то более мощное, с заделом на будущее.
- Плата управления. Я использую RAMPS 1.4, которая прекрасно работает в связке с Arduino Mega. Более дорогая, но более надежная плата — Shield, которая уже совмещает в себе процессорную плату и плату управления. В современных реалиях рекомендую обратить внимание именно на нее. В довесок к ней нужно приобрести минимум 5 микрошаговых контроллеров шаговых двигателей, например — А4988. И лучше иметь пару таких в запасе для замены.
- Стол с подогревом. Это часть, на которой будет находиться печатаемый элемент. Подогрев необходим из-за того, что большинство пластиков не будут держаться на холодной поверхности. Например, для печати PLA пластиком необходимая температура поверхности стола составляет 60-80°C, для ABS — 110-130°C, а для поликарбоната она будет еще выше
В выборе стола тоже есть два варианта — подешевле и подороже. Дешевые варианты, по сути, представляют собой печатные платы с проложенной разогреваемой проводкой. Для эксплуатации на стол такого типа потребуется класть боросиликатное стекло, которое будет царапаться и трескаться в процессе эксплуатации. Поэтому лучшее решение — стол из алюминия. - Шаговые двигатели. Для большинства моделей, включая i2 и i3, используются двигатели типового размера NEMA 17: два для оси Z и по одному для осей X и Y. Готовые экструдеры обычно идут со своим шаговым двигателем в комплекте. Двигатели лучше брать мощные с током в обмотке двигателя от 1А и более, чтобы мощности хватило для подъема экструдера и печати без пропуска шагов на высокой скорости.
- Базовый комплект пластиковых креплений.
- Ремень и шестеренки для его привода.
Примеры внешнего вида элементов: 1) экструдер MK8; 2) процессорная плата Arduino; 3) плата управления RAMPS; 4) контроллеры двигателей; 5) алюминиевый стол с подогревом; 6) шаговый двигатель NEMA 17; 7) набор пластиковых креплений; 8) шестерни привода; 9) ремень привода
Это перечень необходимых к покупке элементов. Хардкорные пользователи могут собирать некоторые из них собственноручно, но новичкам я настоятельно рекомендую приобрести уже готовые решения.
Да, еще будет нужна различная мелочевка (шпильки, подшипники, гайки, болты, шайбы...) для сборки корпуса. На практике оказалось, что использование стандартной шпильки м8 приводит к низкой точности печати на оси Z. Я бы порекомендовал сразу заменить ее на трапециевидную того же размера.
Трапециевидная шпилька м8 для оси Z, использование которой сэкономит вам кучу времени и нервов. Доступна для заказа на всех крупных онлайн-площадках
Также необходимо приобрести адаптированные пластиковые детали для оси X, например, эти из комплекта модификации MendelMax.
Большинство деталей доступно в ближайшем строительном магазине. На RepRap можно найти полный список нужных мелочей со всеми размерами и схемами. Нужный вам комплект будет зависеть от выбора платформы (о платформах поговорим дальше).
Что сколько стоит
Прежде чем углубиться в некоторые аспекты сборки, давайте разберемся, во сколько же обойдется такое развлечение для вашего кошелька. Ниже — перечень необходимых к покупке деталей с усредненной ценой.
Деталь | Количество, ед. | Средяя стоимость, USD |
Экструдер МК8 | 1 | 17 |
Экструдер МК10 | 1 | 45 |
Стол с подогревом | 1 | 11 |
Плата Arduino | 1 | 10 |
Плата RAMPS 1.4 с драйверами | 1 | 10 |
Двигатель NEMA 17 | 4 | 7 |
END-стопы (концевики) | 3 | 1 |
Набор пластиковых креплений | 1 | 30 |
Приводной ремень G2 | 2 | 1 |
Шестеренки для валов двигателей | 2 | 1 |
Шпильки м8 | 2 | 10 |
Шестеренки для валов двигателей | 2 | 1 |
Катушка пластика для печати | 1 | 12 |
Итого с МК8 | 135 | |
Итого с МК10 | 163 |
В таблице представлены примерные цены основных компонентов. Также не забудьте о гайках, шайбах, подшипниках. Эти мелочи могут потянуть еще на $20-30.
Выбор платформы
Для сборки принтеров сообщество уже разработало ряд различных платформ — наиболее оптимальных конструкций корпуса и расположения основных элементов, поэтому изобретать велосипед вам не придется.
Ключевыми платформами для корпусов самосборных принтеров являются i2 и i3. Также существует множество их модификаций с различными улучшениями, но начинающим рассматривать следует именно эти две классические платформы, так как они не требуют особых навыков и тонкой настройки.
Собственно, иллюстрация платформ: 1) платформа i2; 2) платформа i3
Из плюсов i2: она обладает более надежной и устойчивой конструкцией, хотя немного сложнее в сборке; шире возможности для дальнейшей кастомизации.
Вариант i3 требует больше специальных пластиковых деталей, которые нужно докупать отдельно, и имеет низкую скорость печати. Однако более прост в сборке и обслуживании, имеет более эстетически приятный внешний вид. За простоту придется платить качеством печатаемых деталей — корпус имеет меньшую, чем i2, устойчивость, что может влиять на точность печати.
Лично я начинал свои опыты в сборке принтеров с платформы i2. О ней и пойдет речь дальше.
Этапы сборки, сложности и улучшения
В данном блоке я затрону только ключевые этапы сборки на примере платформы i2. Полные пошаговые инструкции можно найти здесь.
Общая схема всех основных компонентов выглядит примерно так. Чего-то особо сложного здесь нет:
Также я рекомендую добавить в вашу конструкцию дисплей. Да, без этого элемента можно легко обойтись, выполняя операции на ПК, но так работать с принтером будет гораздо удобнее.
Понимая, как будут связаны все компоненты, переходим к механической части, где у нас есть два основных элемента — рама и координатный станок.
Собираем раму
Детальная инструкция по сборке рамы доступна на RepRap. Из важных нюансов — вам потребуется набор пластиковых деталей (об этом я уже говорил выше, но лучше повторюсь), который вы можете либо приобрести отдельно, либо попросить напечатать товарищей, у которых уже есть 3D-принтер.


Каркас i2 является довольно устойчивым благодаря форме трапеции.
Вот так выглядит каркас с уже частично установленными деталями. Для большей жесткости я укрепил конструкцию листами фанеры
Координатный станок
На эту деталь крепится экструдер. За ее движение отвечают шаговые двигатели, отображенные на схеме выше. После установки необходима калибровка по всем основным осям.



Из важного — вам потребуется приобрести (или же самостоятельно изготовить) каретку для передвижения экструдера и крепление для приводного ремня. Приводной ремень я рекомендую GT2.
Каретка, напечатанная принтером с предыдущей картинки, после завершения его сборки. На деталь уже установлены подшипники LM8UU под направляющие и крепление для ремня (сверху)
Калибровка и настройка
Итак, мы произвели процесс сборки (как и говорил, у меня он занял 150 часов) — каркас собран, станок установлен. Теперь еще один важный шаг — калибровка этого самого станка и экструдера. Здесь тоже есть маленькие тонкости.
Настраиваем станок
Я рекомендую проводить калибровку станка при помощи электронного штангенциркуля. Не поскупитесь на его приобретение — вы сэкономите много времени и нервов в процессе.
На скрине ниже отображены правильные константы для прошивки Marlin, которые нужно подобрать, чтобы установить корректное количество шагов на единицу измерения. Считаем коэффициент, перемножаем, подставляем в прошивку, после чего заливаем ее на плату.
Константы для прошивки Marlin
Для качественной калибровки я рекомендую в замерах опираться на цифры побольше — брать не
Калибруем экструдер
Когда собран каркас, станок откалиброван, мы приступаем к настройке экструдера. Здесь тоже не все так просто. Основная задача данной операции — правильно отрегулировать подачу пластика.
Если подача недостаточная, то напечатанный тестовый предмет будет с заметными пробелами, как тестовый кубик 1. И наоборот, результат будет выглядеть раздутым при чрезмерной подаче пластика (кубик 2)
Приступаем к печати
Нам остается запустить какой-нибудь CAD или загрузить уже готовые .stl, которые описывают структуру печатаемого материала. Далее эту структуру необходимо преобразовать в набор команд, понятных нашему принтеру. Для этого я использую программу Slicer. Ее тоже нужно корректно настроить — указать температуру, размер сопла экструдера. После этого данные можно отправлять на принтер.
Интерфейс Slicer
В качестве сырья для печати я рекомендую начать с обычного ABS-пластика — он довольно крепкий, изделия из него долговечны, а для работы с ним не требуется высоких температур. Для комфортной печати ABS-пластиком стол нужно разогреть до температуры
Немного важных мелочей. Перед печатью откалибруйте станок по оси Z. Сопло экструдера должно находиться примерно в половине миллиметра от стола и ездить вдоль него без перекосов. Для такой калибровки лучше всего подойдет обычный лист бумаги формата А4, вставленный между соплом и поверхностью стола с подогревом. Если лист можно двигать с незначительным усилием, калибровка выполнена правильно.
Еще один момент, о котором не стоит забывать — обработка поверхности стола с подогревом. Обычно перед печатью поверхность стола покрывают чем-то, к чему хорошо пристает разогретый пластик. Для ABS-пластика это может быть, например, каптоновый скотч. Минусом скотча является необходимость его переклеивать через несколько циклов печати. Кроме этого, придется буквально отдирать от него приставшую деталь. Все это, поверьте, отнимает много времени. Поэтому, если есть возможность избежать этой возни, лучше ее избежать.
Альтернативный вариант, который я использую вместо скотча — нанесение нескольких слоев обычного светлого пива с последующим нагревом стола до
После того как мы все собрали и настроили, можно приступать к печати. Если у вас есть ЖК-экран, то файл можно передать на печать при помощи обычной SD-карты.
Первые результаты могут иметь неровности и другие артефакты — не расстраивайтесь, это нормальный процесс «притирки» элементов принтера, который закончится спустя несколько циклов печати.
Рекомендации, которые смогут упростить жизнь (а иногда — сэкономить деньги)
Кроме небольших рекомендаций, приведенных в тексте выше, в этом разделе я дам еще краткий перечень советов, которые значительно упростят эксплуатацию 3D-принтера и жизнь его владельца.
- Не экспериментируйте с форсунками. Если вы планируете сразу печатать из материалов, которые требуют высоких температур, то лучше сразу возьмите экструдер МК10. На МК8 можно «навесить» специальные форсунки, поддерживающие высокотемпературные режимы. Но такие модификации часто вызывают сложности и требуют особого опыта. Лучше избежать этой возни еще «на берегу», просто поставив подходящий для вас экструдер.
- Добавьте реле стартера для стола с подогревом. Усовершенствование системы питания этой важной для печати детали при помощи реле стартера поможет решить известную проблему RAMP 1.4 — перегрев транзисторов, управляющих питанием стола, который может привести к выходу платы из строя. Я сделал такой апгрейд после того, как пришлось выбросить несколько RAMPS 1.4.
- Выберите правильный диаметр пластика для печати. Рекомендую брать пластик диаметром 1,75 мм для MK8 и MK10. Если взять пластик, например, в 3 мм, то экструдеру просто не хватит сил, чтобы проталкивать его с приемлемой скоростью — печататься все будет значительно дольше, а качество упадет. Для MK8 идеально подходит ABS-пластик, MK10 сможет производить изделия из поликарбоната.
- Используйте только новые и точные направляющие по осям X и Y. Это влияет на качество печати. Сложно рассчитывать на хорошее качество при гнутых или деформированных направляющих по осям.
- Позаботьтесь об охлаждении. В ходе моих экспериментов с различными экструдерами лучшие результаты показал МК10 — он печатает довольно точно и быстро. Также МК10 может печатать пластики, требующие более высокой температуры печати, чем ABS, например поликарбонат. Хоть он и не так сильно подвержен перегреву, как его младший брат МК8, все же я рекомендую позаботиться о его охлаждении, добавив в вашу конструкцию кулер. Он должен быть постоянно включен, эту опцию можно настроить в Slicer. Также можно добавить кулеры для поддержания приемлемой температуры шаговых моторов, однако следите, чтобы их потоки воздуха не попадали на печатаемую деталь, так как это может привести к ее деформации из-за слишком быстрого охлаждения.
- Предусмотрите сохранение тепла. Да, с одной стороны, мы боремся с перегревом элементов. С другой — равномерная температура вокруг принтера будет способствовать качественной печати (пластик будет более податливым). Для достижения равномерной температуры можно поставить наш принтер, например, в картонную коробку. Главное — перед этим подключить и настроить кулеры, о чем написано выше.
- Подумайте о термоизоляции стола. Стол с подогревом нагревается до больших температур. И если часть этого тепла уходит с толком, подогревая печатаемую деталь, то вторая часть (снизу) — просто уходит вниз. Чтобы сконцентрировать тепло от стола на детали, можно провести операцию по его термоизоляции. Для этого я просто креплю к его нижней части пробковый коврик для мыши при помощи канцелярских зажимов.
Выводы
Уверен, в процессе сборки вы столкнетесь с рядом трудностей, присущих именно вашему проекту. От этого не застрахуют ни этот текст, ни даже самые подробные гайды.
Как я и написал во вступительной части, изложенное не претендует на статус детального мануала по сборке. Описать все-все этапы и их тонкости практически невозможно в рамках одного такого текста. Прежде всего, это обзорный материал, который поможет вам подготовиться к процессу сборки (как мысленно, так и материально), понять, нужно ли лично вам заморачиваться самосбором — или же махнуть на все рукой и купить готовое решение.
Для меня сборка принтеров стала увлекательным хобби, которое помогает закрывать некоторые вопросы в домашних и рабочих делах, отвлечься от программирования и сделать что-то интересное своими руками. Для моих детей — развлечением и возможностью получить необычные и уникальные игрушки. Кстати, если у вас есть дети, которым возраст позволяет возиться с подобными штуками, такое занятие может стать хорошим подспорьем для входа в мир механики и технологий.
Для каждого векторы использования 3D-принтеров будут самыми разными и весьма индивидуальными. Но, если уж вы решитесь посвятить личное время такому увлечению, поверьте, обязательно найдете, что печатать :)
Буду рад ответить на комментарии, замечания и вопросы.
Что почитать/посмотреть
- что можно напечатать;
- форум по 3D-принтерам;
- сайт сообщества RepRap с описанием моделей и инструкциями по сборке;
- принтер, который печатает электронику.
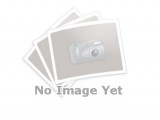
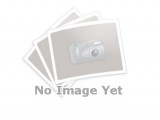